Simulation
Simulation
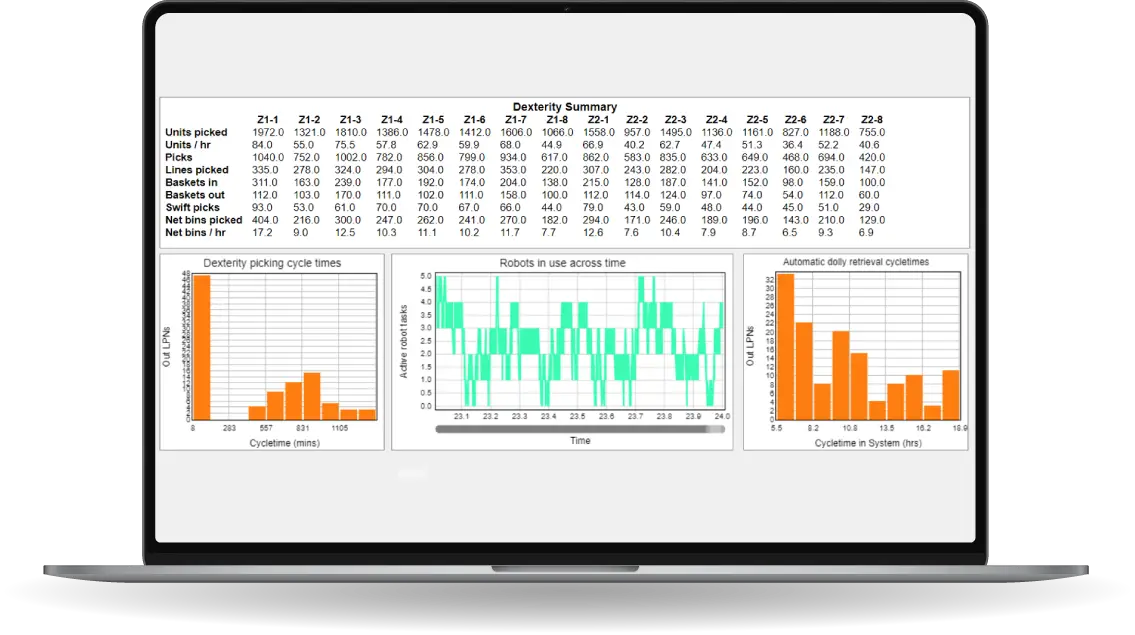
Our supply chain simulation services are designed to help companies make informed decisions before investing large sums of capital.
Frequently Asked Questions
·Can I validate the capacity layout with automation before committing to a PO?
·What are the risks and financial impacts of modifying our supply chain (production, inventory, transportation, product portfolio, etc.)?
·What is the maximum processing capacity of the new layout or automation we want to implement?
·What is the right amount of inventory for each SKU?
·What is the most efficient production plan?
·How many forklifts or AGVs do I require for my forecasted volume?
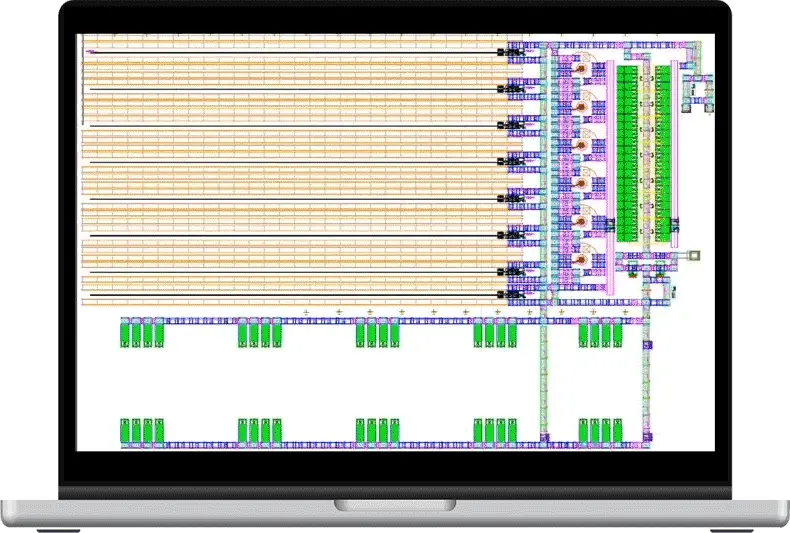
We use advanced simulation tools and techniques to model actual operations with high levels of complexity in record times. We recognize FlexSim® as the best in class software for simulating supply chain processes.
Our Simulation Times
Picking
Processes
4 Weeks
Distribution
Center
6 Weeks
Manufacturing
Plant
12 Weeks
Footprint
12 Weeks
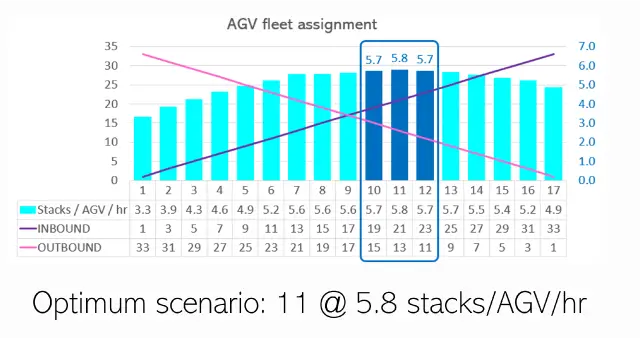
Our approach allows customers to experiment and test different scenarios, giving them the confidence they need to make critical business decisions.
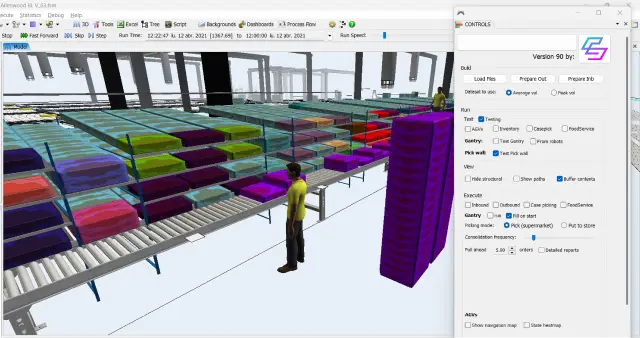
We also commission the model to the customer, allowing them to continue experimenting and testing on their own.
Simulation Resources
Start building a model sometimes requires inspiration. Use these mods to speed up this process. Click on the one that interests you.
With our simulation services, companies can make informed and confident decisions, knowing that they have tested and validated their plans before investing.
We have experience simulating:
·Manual distribution centers
·Just in time, just in sequence, kan-ban
·Warehouse and picking area slotting
·Distributed inventory policies / levels
·A-frame, ASRS, multishuttle, AGVS, gantry picking, sorters
·Pick to belt, bucket brigades, goods to person
·Yard and transit inside a facility
·Distribution network design or optimization
Simulation Case Studies
Laval MTH
Name: Minimum Tray Handling
Industry: Food
Partner: Extra-DC Transport
Model Type: Strategic model for feasibility estimation and operational model definition
Technology: Storage in multishuttle, automated sorting of plastic trays, manual sorting at ergonomic stations
The model was used in Canada to evaluate the benefits of integrating inbound flows from on-site manufacturing and external plants for order preparation across various channels.
Pallets are automatically deconsolidated and stored in pairs using a 12-level multishuttle system. This deconsolidation is crucial for the subsequent preparation of low-volume orders for a wide product portfolio.
Product sorting is 90% automated, using sorting cells supplied in the correct sequence to 2 automatic palletizers and an additional manual cell for sorting corrugated materials and/or individual parts.
Sorting is done at height, so when the pallets are complete, they are wrapped and delivered for routing to the scheduled shipping zone for each shipment (route).
Lala
Name: Manual Sorting of Boxes and Pieces
Industry: Dairy
Partner: NetLogistik
Model Type: Manual sorting process of pieces in a sorting tower and box sorting in high-density racks
Technology: Voice picking, conveyor belt, sorting tower, pushback racks
The model shows the refrigerated distribution center of Lala Norte located in Vallejo, Mexico City. The new layout is designed to maximize the productivity of box sorting and piece sorting into plastic totes for greater control and productivity.
- Operators carry out the sorting of corrugated materials using a voice picking system, z-pick in narrow aisles, and direct rack picking. High-movement products are sorted from pushback racks, while slow-moving products are sorted from selective racks.
- The sorting of fractional boxes is performed in a three-level sorting tower, facilitated by a central conveyor belt. Each order starts with one or more empty plastic totes on the 3rd level and moves through the sorting zones using a pick-n-pass process. Optimal balancing of these zones is crucial.
Coca Cola
Name: Family-Based Picking Tunnel
Industry: Beverages
Partner: Unik
Model Type: Automation of picking process in warehouse
Technology: ASRS miniload, pushback rack
The model shows a picking tunnel, where box sorting occurs on the ground floor with products organized by family. Above the picking tunnels, the storage cube is utilized using push-back racks managed by forklifts. The replenishment of medium and slow-moving products is done automatically from a central sub-module that includes a box warehouse and a crane (ASRS miniload). There are multiple benefits to such a system:
- Products are organized by families to prevent damage and to require minimal reorganization upon arrival at the point of sale.
- High-volume products have multiple pallet positions (reducing waiting times for replenishment), and low-volume products are organized in carton flow racks to maximize the density of picking faces (reducing the linear distance the picker needs to walk).
In the presence of voice technology or PTL, a highly organized layout like this, equipped with continuous replenishment, leads to a significant boost in productivity.